Cement to kluczowy materiał budowlany wytwarzany z surowców mineralnych. W procesie jego produkcji wykorzystuje się głównie wapień, margiel i glinę. Cały proces produkcyjny składa się z siedmiu głównych etapów, począwszy od wydobycia surowców, a skończywszy na pakowaniu gotowego produktu.
To materiał hydrauliczny, który po zmieszaniu z wodą twardnieje. Temperatura wypalania sięga 1450°C, co jest niezbędne do uzyskania odpowiednich właściwości. Jego skład chemiczny bazuje na tlenkach wapnia, krzemu, glinu i żelaza.
Kluczowe informacje:- Produkcja rozpoczyna się od wydobycia surowców w kopalniach odkrywkowych
- Mączka piecowa powstaje przez zmielenie surowców z dodatkami
- Klinkier to kluczowy półprodukt powstający w piecu obrotowym
- Do klinkieru dodaje się gips jako regulator czasu wiązania
- Cement można modyfikować różnymi dodatkami dla uzyskania specyficznych właściwości
- To podstawowy składnik betonu i zapraw murarskich
- Proces produkcji jest wieloetapowy i wymaga precyzyjnej kontroli
Co to jest cement i z czego się składa
Cement to podstawowy materiał wiążący stosowany w budownictwie. Powstaje poprzez zmielenie klinkieru portlandzkiego z dodatkiem regulatora czasu wiązania - gipsu. Jest to materiał hydrauliczny, co oznacza, że reaguje z wodą tworząc trwałe połączenia. To właśnie dzięki tej właściwości cement stanowi kluczowy składnik betonu i zapraw budowlanych.
W procesie produkcji cementu kluczową rolę odgrywają minerały klinkierowe. Są one odpowiedzialne za właściwości wiążące i wytrzymałościowe gotowego produktu. Temperatura wypalania sięgająca 1450°C sprawia, że surowce przechodzą szereg przemian chemicznych, tworząc aktywne związki mineralne.
- Tlenek wapnia (CaO) - 60-67%
- Ditlenek krzemu (SiO₂) - 17-25%
- Tlenek glinu (Al₂O₃) - 4-8%
- Tlenek żelaza (Fe₂O₃) - 2-5%
- Siarczan wapnia (CaSO₄) - 3-5%
Surowce wykorzystywane do produkcji cementu
Do wytwarzania cementu używa się głównie surowców naturalnych. Podstawowym składnikiem jest wapień, który dostarcza tlenku wapnia. Drugim ważnym surowcem jest glina, będąca źródłem krzemionki, tlenku glinu i żelaza. Dodatkowo stosuje się margiel, który jest naturalną mieszaniną węglanu wapnia i minerałów ilastych. Gips dodawany jest jako regulator czasu wiązania.
Surowiec | Udział procentowy |
Wapień | 75-80% |
Glina | 15-20% |
Dodatki korygujące | 3-5% |
Gips | 2-3% |
Czytaj więcej: Z czego jest cement: poznaj wszystkie składniki oraz ich właściwości
Proces wydobycia surowców do produkcji cementu
Proces produkcji cementu rozpoczyna się od wydobycia surowców w kopalniach odkrywkowych. Wydobycie prowadzi się metodą strzałową lub przy użyciu koparek mechanicznych. Transport urobku odbywa się za pomocą taśmociągów lub specjalistycznych pojazdów ciężarowych.
Nowoczesne metody wydobywcze pozwalają na precyzyjną selekcję materiału. Każda partia surowca jest badana pod kątem składu chemicznego. To zapewnia odpowiednią jakość materiału wyjściowego do dalszej produkcji cementu.
Przygotowanie i rozdrabnianie materiałów
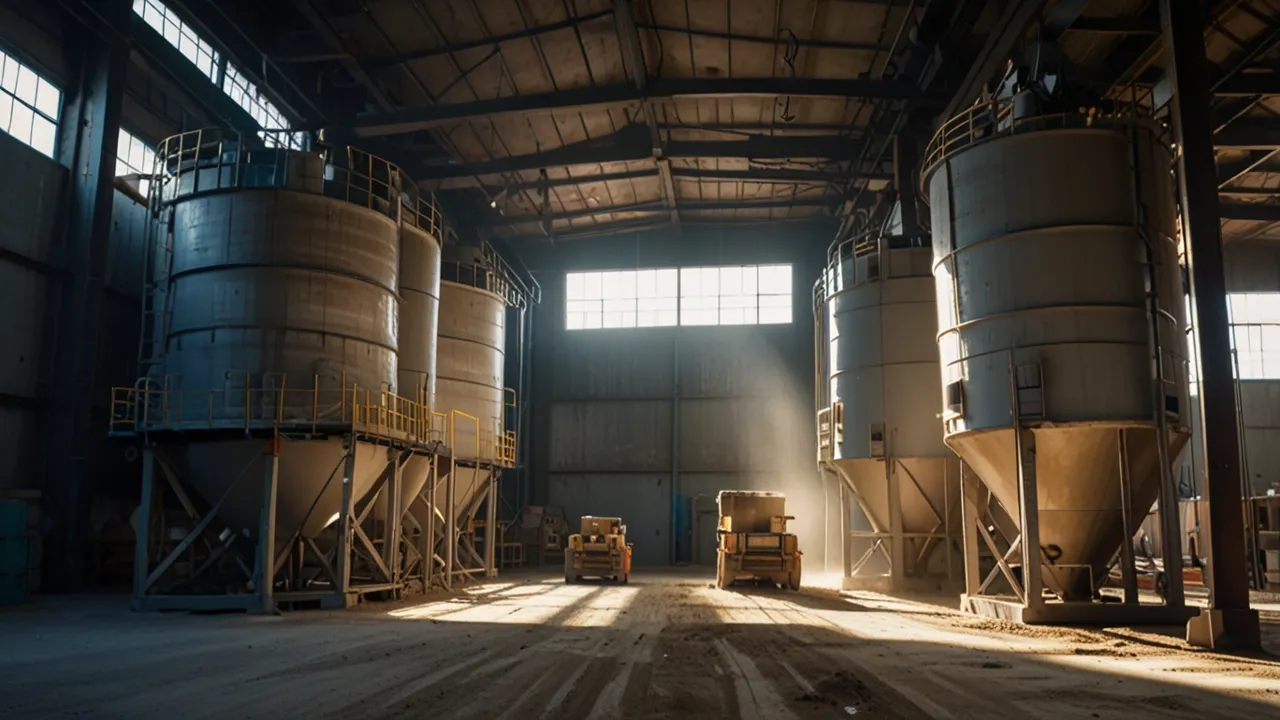
Wydobyte surowce trafiają do kruszarek, gdzie następuje ich wstępne rozdrobnienie. Materiał jest kruszony do wielkości około 5 centrymetrów. Proces ten jest kluczowy dla efektywności dalszych etapów produkcji cementu.
Po rozdrobnieniu materiał przechodzi proces homogenizacji. Surowce są mieszane w odpowiednich proporcjach w specjalnych silosach homogenizacyjnych. To zapewnia jednolity skład chemiczny mieszanki, co jest niezbędne dla utrzymania stałej jakości powstającego cementu.
Etap mielenia surowców
Proces produkcji cementu wymaga dokładnego zmielenia wszystkich składników. W młynach kulowych lub walcowych materiał jest mielony do postaci mączki. Powstała mączka ma konsystencję bardzo drobnego proszku, gdzie 85% cząstek jest mniejszych niż 90 mikrometrów.
- Piasek kwarcowy - korekcja zawartości krzemionki
- Popioły lotne - poprawa urabialności
- Ruda żelaza - regulacja modułu żelazowego
- Boksyt - zwiększenie zawartości tlenku glinu
Wypalanie klinkieru - najważniejszy etap produkcji
Wypalanie to kluczowy etap w procesie produkcji cementu. Mączka surowa trafia do pieca obrotowego, gdzie temperatura sięga 1450°C. W tak wysokiej temperaturze zachodzą reakcje chemiczne, które prowadzą do powstania klinkieru cementowego.
W piecu następuje szereg przemian fazowych. Materiał przechodzi przez strefy o różnych temperaturach, gdzie kolejno następuje odparowanie wody, rozkład węglanów i tworzenie się minerałów klinkierowych. To właśnie te minerały odpowiadają za właściwości wiążące powstającego cementu.
Nowoczesne piece obrotowe są wyposażone w systemy odzysku ciepła. Gorące gazy z pieca podgrzewają wstępnie mączkę surową, co znacząco zwiększa efektywność energetyczną całego procesu produkcji cementu.
Proces chłodzenia klinkieru
Po wytworzeniu cementu w piecu, gorący klinkier musi zostać schłodzony. Proces chłodzenia odbywa się w specjalnych chłodnikach rusztowych, gdzie temperatura spada z 1450°C do około 100°C. To kluczowy moment dla jakości produktu.
Szybkość chłodzenia wpływa na strukturę krystaliczną klinkieru. Odpowiednie chłodzenie zapewnia zachowanie pożądanych właściwości minerałów klinkierowych, co przekłada się na końcową jakość cementu.
Końcowe mielenie i dodatki
Schłodzony klinkier jest mielony wraz z dodatkami w młynach kulowych. Na tym etapie produkcji cementu dodawany jest gips, który reguluje czas wiązania. Proces mielenia trwa do momentu uzyskania odpowiedniej powierzchni właściwej ziaren.
W zależności od przeznaczenia cementu, do mielenia wprowadzane są różne dodatki mineralne. Mogą to być popioły lotne, żużel wielkopiecowy czy dodatki pucolanowe. Każdy z nich nadaje końcowemu produktowi specyficzne właściwości.
Pakowanie i transport gotowego cementu
Gotowy cement jest przechowywany w specjalnych silosach. Transport produktu odbywa się na dwa sposoby: luzem lub w workach. Cement luzem jest przewożony w specjalistycznych cysternach samochodowych lub kolejowych bezpośrednio do odbiorców.
Pakowanie cementu w worki odbywa się na automatycznych liniach pakujących. Każdy worek jest szczelnie zamykany i oznaczany informacjami o rodzaju produktu, dacie produkcji i warunkach przechowywania.
Rodzaj opakowania | Zastosowanie |
Worki 25 kg | Drobne prace budowlane |
Worki typu Big-Bag (1000 kg) | Średnie inwestycje |
Transport luzem | Duże projekty budowlane |
Kontrola jakości w procesie produkcji
Jak powstaje cement wysokiej jakości? Kluczem jest stała kontrola na każdym etapie produkcji. Próbki są pobierane i badane w laboratorium już od momentu wydobycia surowców. Każda partia mączki surowej przechodzi szczegółową analizę składu chemicznego.
W trakcie procesu produkcji cementu kontrolowane są parametry technologiczne: temperatura wypalania, czas przebywania materiału w piecu, oraz skład chemiczny klinkieru. Gotowy produkt jest badany pod kątem wytrzymałości, czasu wiązania i zgodności z normami. Laboratorium pracuje w trybie ciągłym, zapewniając stałą kontrolę jakości.
Nowoczesne technologie w produkcji cementu
Współczesne wytwarzanie cementu wykorzystuje zaawansowane technologie. Piece obrotowe są wyposażone w systemy automatycznego sterowania, które optymalizują proces wypalania. Wprowadzane są również rozwiązania związane z wykorzystaniem paliw alternatywnych.
Innowacje w procesie produkcji cementu skupiają się na zwiększeniu efektywności energetycznej i redukcji emisji CO2. Wykorzystuje się systemy odzysku ciepła, zaawansowane filtry odpylające oraz technologie pozwalające na wykorzystanie surowców z recyklingu. Automatyzacja i cyfryzacja procesu produkcyjnego pozwala na precyzyjne sterowanie każdym etapem produkcji.
Jak nowoczesne technologie kształtują produkcję cementu
Proces produkcji cementu to złożony ciąg technologiczny, który łączy tradycyjne metody z nowoczesnymi rozwiązaniami. Od wydobycia surowców, przez wypalanie klinkieru w temperaturze 1450°C, aż po końcowe mielenie - każdy etap jest precyzyjnie kontrolowany i optymalizowany.
Współczesne cementownie stawiają na automatyzację procesu produkcyjnego i dbałość o środowisko. Wykorzystują zaawansowane systemy filtracji, odzysku ciepła i kontroli jakości. To sprawia, że powstający cement spełnia najwyższe standardy jakościowe przy jednoczesnej minimalizacji wpływu na otoczenie.
Najważniejszym elementem całego procesu jest wypalanie klinkieru, które decyduje o właściwościach końcowego produktu. To właśnie na tym etapie powstaje cement o określonych parametrach, które później można modyfikować poprzez dodatki wprowadzane podczas końcowego mielenia.